When To Run Pid Auto Tune
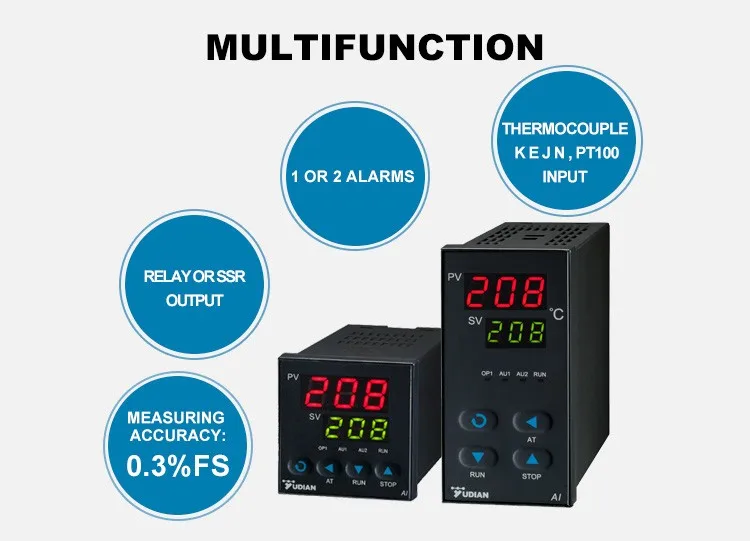
A self-tuning PID demonstration GPL software using genetic algorithm.
In my OctoPrint temp graph I see the temp is over-shooting quite a bit on the hot-end, so I attemped to run M303 E0 S220 C8 multiple times. Each time autotune fails with 'temp too high'. Autotune ran fine on my MK2S, but fails consistently on the MK3. What can I do to get PID autotune to run so I can get my hot-end temp to run more evenly?. Oct 01, 2006 An engineer would run a Ziegler-Nichols test, record the control effort and resulting process variable on a strip chart, divine the behavior of the process from trend line shapes, tune the loop to match the process, then start production with the new loop in automatic mode.
PID Tune to your hotend will result in better quality prints so it’s worth the time to learn how to do it. It’s not that hard at all. If you haven’t installed the Marlin Firmware on your 3D Printers Mainboard or don’t know what Marlin is check out my article; Beginner Guide to Marlin 1.1 3D Printer Firmware before trying this tutorial. Jan 17, 2012 You can tune again at a higher setpoint after confirming that tuning won’t cause the temperature to go too high. There is probably a time limit on the auto tune function, so very slow processes may not tune. Check the PID settings prior to and after tuning. If they do not change, the auto tuning process failed for one reason or another. When the experiment ends, the block calculates PID gains and returns them at the pid gains port. For a more detailed example of a Simulink model configured for closed-loop PID autotuning, see Tune PID Controller in Real Time Using Closed-Loop PID Autotuner Block. Bumpless Transfer for Open-Loop Tuning.
Demonstration video here : https://www.youtube.com/watch?v=cK6kWN9K_do
Explanation here : https://kevinjoly25.wordpress.com/2015/01/13/pid-controller-auto-tuning-using-genetic-algorithm/
- Qt4
$ mkdir build
$ cd build
$ cmake .
$ make
No install method has been provided yet. However, you can run the software from the build directory:$ ./pid-autotune
There is 4 dock widgets in this software:
- Motor: enable the user to choose a motor to use and test it in closed on opened loop.
- Controller : enable the user to choose a controller to use with the motor (check 'Use controller'). The controller parameters can be set in this widget for test purpose.
- Graph settings : enable the user to change the axes scale by setting the min and max to be displayed.
- Genetic : enable the user to control the genetic algorithm parameters such as:
- input : value of the input applied on the system.
- min/max Kx : boundary values of each PID action.
- Evaluation time : system running time when evaluating fitness.
- Population size : size of the genetic algorithm's population.
- Mutation ratio : probability to mutate the offspring's variable.
- Crossover ratio : probability to crossover two parents.
- Overshoot penalty : ratio which multiply the error when an overshoot occurs. If you don't want any overshoot, set this to the maximum.
- Elite num : Number of best parents kept in the next generation of population.The start button launch the genetic process. Pause stop the process, press start to launch it again without any loss. Reset enable the user to generate a new random population by deleting the old one.
Example
- Under 'Motor' : choose the DummyMotor.
- Under 'Graph settings' : set xMax to 0.1 and yMax to 2.0.
- Under 'Genetic' : set maxKp to 1.0, maxKd to 2.0, maxKi to 0.1.
- Hit start button and enjoy the dance of a self-tuning PID! ;)
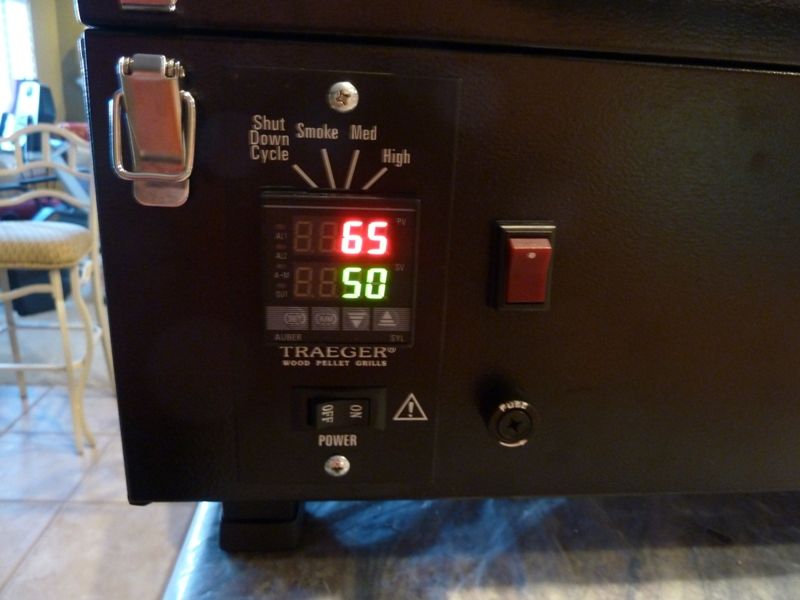
More on GAs..
The fitness function is using the sum of squarred error to evaluate the generated PID.Thanks to this fitness function, tournament selection can be used in order to select parents of the next PID population.The genetic algorithm implemented in Genetic.cpp uses arithmetic crossover and gaussian mutation to generate the new population.Elitism can be used.
This software is using the GPL software QCustomPlot from Emanuel Eichhammer.
PID Autotuning for a Plant Modeled in Simulink
To use PID autotuning for a plant modeled in Simulink®, you incorporate a PID autotuner block into the model. You can control the autotuning process while the model is running. When tuning is complete you can validate tuned controller parameters against the simulated plant. Using PID autotuning this way can be useful for generating an initial PID design that you later refine with real-time autotuning.
Workflow for Autotuning in Simulink
The following steps provide a general overview of the workflow for PID autotuning in Simulink using the Closed-Loop PID Autotuner or Open-Loop PID Autotuner blocks.
Incorporate a PID autotuner block into your model between the PID controller and the plant.
Configure the start/stop signal that controls when the tuning experiment begins and ends.
Specify controller parameters such as controller type and the target bandwidth for tuning.
Configure experiment parameters such as the amplitudes of the perturbations injected during the frequency-response experiment.
Run the model and initiate tuning. Use the start/stop signal to initiate the PID autotuning process. When you start the process, the autotuner block injects test signals and measures the response of the plant.
Stop the experiment with the start/stop signal. When the experiment stops, the autotuner block computes and returns tuned PID gains. You can examine the tuned gains for reasonableness.
Transfer the tuned gains from the autotuner block to your PID controller. You can then validate the performance of the tuned controller in Simulink.
Step 1. Incorporate Autotuner into Model
The following illustration shows one way to incorporate a Closed-Loop PID Autotuner block in between your PID controller and your plant.
The control signal u
from the PID controller feeds into the u port of the autotuner block. The u+Δu port feeds into the plant input. Before you begin the autotuning process, the autotuner block feeds the PID control signal directly from u to u+Δu and the plant input. In that state, the autotuner block has no effect on plant or controller behavior. During the autotuning process, the block injects test signals at the plant input and measures the response at y
.
The start/stop
signal controls when the autotuning process begins and ends (see Step 2. Configure Start/Stop Signal). When the experiment ends, the block calculates PID gains and returns them at the pid gains
port.
For a more detailed example of a Simulink model configured for closed-loop PID autotuning, see Tune PID Controller in Real Time Using Closed-Loop PID Autotuner Block.
Bumpless Transfer for Open-Loop Tuning
When To Run Pid Autotune Video
The Open-Loop PID Autotuner block opens the loop between u and u+Δu during the estimation experiment. If your controller includes integral action, you can use signal tracking to avoid integrator windup while the loop is open. Signal tracking enables the PID controller to continue to track the real plant input while it is out of the loop. Without it, your system can experience a bump when the control loop is closed at the end of the tuning process. In system of the following illustration, the PID controller is a Simulink PID Controller block with the Enable tracking mode parameter on. The plant input feeds into the tracking input of the controller block.
For a more detailed example of a Simulink model configured for open-loop PID autotuning, see Tune PID Controller in Real Time Using Open-Loop PID Autotuner Block.
Step 2. Configure Start/Stop Signal
To start and stop the autotuning process, use a signal at the start/stop
port. When the experiment is not running, the block passes signals unchanged from u to u+Δu. In this state, the block has no impact on plant or controller behavior.
Feb 17, 2014 If you want to know how to Auto-Tune your voice/audio on GarageBand, then this short tutorial will you demonstrate how to quickly and efficiently apply this technique to your videos. Imovie how to add music. Nov 10, 2010 just found out.idk if it works with iMovie 09. How to Gain Instagram Followers Organically 2019 (Grow from 0 to 5000 followers FAST!).
The frequency-response estimation experiment begins and ends when the block receives a rising or falling signal at the start/stop
port, respectively. In the systems illustrated in Step 1. Incorporate Autotuner into Model, the start/stop signal is a simple switch. While the model is running, you can use the switch to begin and end the experiment. When you end the experiment, the algorithm generates the tuned PID gains and the block returns them at the pid gains
port.
As an alternative to a manual switch, you can configure the start/stop
signal to begin and end the experiment automatically at particular simulation times. For example, you can use the sum of two Step blocks: Configure one Step block to step from 0 to 1 at the experiment start time, and a second Step block to step from 1 to 0 at the end time. Feed the sum of the two signals into the start/stop
port of the PID autotuner block.
You can configure any other logic appropriate for your application to control the start and stop times of the experiment. For more information about when to start and stop the experiment, see Step 5. Run Model and Initiate Tuning Experiment.
Step 3. Specify Controller Parameters and Tuning Goals
In the PID autotuner block, specify the configuration of the PID controller you are tuning, using the following block parameters:
Type
Form
Time Domain
Controller sample time (sec)
Integrator method
Filter method
Then, specify the target bandwidth and phase margin for tuning with the Target bandwidth (rad/sec) and Target phase margin (degrees) parameters, respectively.
The target bandwidth is the target value for the 0-dB gain crossover frequency of the tuned open-loop response CP, where P is the plant response, and C is the controller response. This crossover frequency roughly sets the control bandwidth. For a desired rise-time τ, a good guess for the target bandwidth is 2/τ.
The target phase margin reflects your desired robustness of the tuned system. Typically, choose a value in the range of about 45°– 60°. In general, higher phase margin improves overshoot, but can limit response speed. The default value, 60°, tends to balance performance and robustness, yielding about 5-10% overshoot, depending on the characteristics of your plant.
For more information about setting these parameters, see the Closed-Loop PID Autotuner or Open-Loop PID Autotuner block reference pages.
Step 4. Set Experiment Parameters
The frequency-response estimation experiment injects sinusoidal signals at frequencies around the target bandwidth ωc:
[1/3, 1, 3, 10]ωc for the Open-Loop PID Autotuner block
[1/10,1/3, 1, 3, 10]ωc for the Closed-Loop PID Autotuner block
Use the Sine Amplitudes parameter of the blocks to specify the amplitudes of these signals.
If your plant is asymptotically stable, the Open-Loop PID Autotuner block can estimate the plant DC gain with a step perturbation. Specify the amplitude of this perturbation with the Step Amplitude parameter. If your plant has a single integrator, clear the Estimate DC gain with step signal parameter.
Caution
Do not use either closed-loop or open-loop PID autotuning with an unstable plant.
Do not use open-loop PID autotuning with a plant that has more than one integrator. You can use closed-loop PID autotuning with a multiple-integrator plant.
All the perturbation amplitudes must be:
Large enough that the perturbation overcomes any deadband in the plant actuator and generates a response above the noise level.
Does post molone use auto tune. Small enough to keep the plant running within the approximately linear region near the nominal operating point, and to avoid saturating the plant input or output.
For more information about setting the experiment parameters, see the Closed-Loop PID Autotuner and Open-Loop PID Autotuner block reference pages.
Step 5. Run Model and Initiate Tuning Experiment
After you have configured all the parameters for tuning, run the model.
If you have configured a manual
start/stop
signal, begin the experiment when your plant has reached steady-state.If you have configured the
start/stop
signal to begin and end the tuning process at specific times, allow the simulation to run long enough to begin the experiment.
Step 6. Stop Experiment and Examine Tuned Gains
The frequency-response estimation experiment ends when the start/stop
signal falls.
If you have configured a manual
start/stop
signal, end the experiment when the signal at the% conv
output stabilizes near 100%.If you have configured the
start/stop
signal to begin and end the tuning process at specific times, allow the simulation to run through the end of the experiment.
In either case, a conservative estimate for the experiment time is 200/ωc for closed-loop tuning or 100/ωc for open-loop tuning, where ωc is your target bandwidth.
When you stop experiment, the block computes new PID gains based on the estimated frequency response of the system and your specified tuning goals. Examine them for reasonableness. For instance, if you have an initial PID controller, you might expect the tuned gains to be roughly the same magnitude as the gains of the initial design. There are several ways to see the tuned gains:
View the output of the
pid gains
port of the autotuner block. One way to view this output is to connect the output to a Simulink Display block.In the block, in the Block tab, click Export to MATLAB. The block creates a structure in the MATLAB® workspace,
OnlinePIDTuningResult
. For more information about the contents of this structure, see the Closed-Loop PID Autotuner or Open-Loop PID Autotuner block reference pages.
Step 7. Update PID Controller with Tuned Gains
The autotuner block can write tuned controller parameters directly to the PID controller block, if your PID controller is either:
A Simulink PID Controller block.
A custom PID controller for which the following conditions are both true:
The custom controller is a masked subsystem.
The PID gains are mask parameters named
P
,I
,D
, andN
. (You do not need to use all four parameters. For example, if you use a custom PI controller, then you only need mask parametersP
andI
.)
To configure the autotuner block to write tuned gains to your controller, designate the controller as the associated PID block in the PID autotuner block parameters. (For more information, see the see the Closed-Loop PID Autotuner or Open-Loop PID Autotuner block reference pages.) Then, update your controller by clicking Update PID Block. You can update the PID gains while the simulation is running. Doing so is useful for immediately validating tuned PID gains.
Note
At any time during simulation, you can change tuning or experiment parameters, start the experiment again, and push the new tuned gains to the PID block. You can then observe the behavior of your plant as simulation continues with the new gains.
Manual Update of PID Gains
If your custom PID controller does not satisfy the conditions for direct update, you must transfer the tuned gains to your controller some other way, such as manually or with your own logic.
When you examine these gains and transfer them to your own controller, be aware of the meaning of these gains in the PID autotuner blocks. In discrete time, the blocks assume the following PID controller transfer function:
in parallel form, or in ideal form,
Fi(z) and Fd(z) depend on the values you specify for the Integrator method and Filter method formulas, respectively. For more details, see the Closed-Loop PID Autotuner or Open-Loop PID Autotuner block reference pages.
See Also
When To Run Pid Auto Tune Download
Closed-Loop PID AutotunerOpen-Loop PID Autotuner